从大自然寻找并提取基因,编程并导入微生物,通过生物发酵在细胞工厂中生产各种产品。被誉为“第三次生物技术革命”的合成生物,正在引领产业技术变革和生物经济发展。
11月14日,在北京市科委、中关村管委会举办的“新质生产力看北京”主题采访中,新京报贝壳财经记者通过实地走访了解到,目前北京合成生物产业正积极突破前沿技术、推动重点品种转化和创新企业落地、布局技术服务平台、加快推动园区建设、提升国际影响力。随着产业发展,相关产业创新成果加速涌现。
截至目前,北京市已集聚80余家合成生物制造领域创新企业,形成充满活力的产业生态。合成生物技术引领下,一幅更清洁、更经济、更高效的工业图景正在徐徐展开。
甘露醇生产成本大幅降低 合成生物技术引领绿色生产路径
走进微元合成生物技术(北京)有限公司(以下简称“微元合成”),一面画满“代谢网络图”的墙,揭示了合成生物技术的底层逻辑。
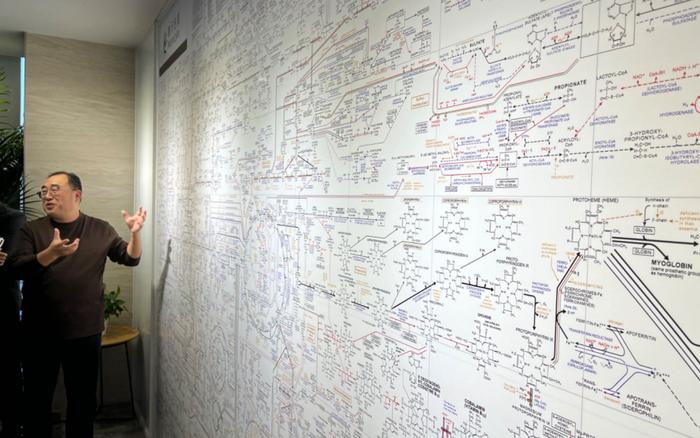
“细胞代谢网络图展示了细胞在酶的催化作用下,利用葡萄糖生成各种物质的代谢过程。合成生物学就是利用基因编辑技术、酶分子改造技术等核心底层技术,设计全新的细胞代谢路径,尽可能让细胞按照我们的意愿高效生产目标产物,以达到更低的生产成本”,微元合成首席创新官刘伟丰对贝壳财经记者介绍。
微元合成成立于2021年12月,核心团队来源于中科院微生物所,是国内最早从事合成生物学研发及产业化的团队之一。公司面向人类营养、动物营养、日化原料、药用原辅料和大宗平台产品市场,采用生物法替代农业生产和化工制造。目前,微元合成的成熟产品管线多达数十项,公司正在推进甘露醇、阿洛酮糖等多个产品管线的商业化落地。
甘露醇被广泛用于原料药、药用辅料和食品添加剂。目前,其工业生产方式主要为化工加氢法。2023年三季度,微元合成首次完成了第一代甘露醇生物制造技术的规模化量产和数百吨销售。
微元合成战略发展总裁崔维敏表示,传统化工加氢法生产甘露醇技术因催化剂的选择性较低,导致甘露醇转化率低、低附加值副产物多的问题,同时还存在重金属和还原糖残留、环境不友好等痛点,而微元合成通过合成生物制造技术可以做到低成本、高效率、无污染地进行甘露醇生产,据介绍,目前团队已完成第五代技术的开发,以国内平均原料和能源成本计算,该方式生产甘露醇的成本低于1万元/吨。
与此同时,目前微元合成开发了全球首创基于生物发酵法量产阿洛酮糖的批量生产技术,在该生产方式下,阿洛酮糖产品纯度达到99.9%,生产成本显著下降。
集聚80余家创新企业 创新成果加速涌现
瞄准合成生物技术和产业变革趋势,积极抢抓全球生物经济发展机遇,北京市抢先布局合成生物赛道。随着合成生物产业的持续发展,北京在该领域的创新资源集聚能力正迅速增强。
今年1月6日,北京市合成生物制造产业创新发展工作推进会成功举办,北京市合成生物制造技术创新中心(筹)正式落地未来科学城。
创新中心落地工作由未来科学城管委会统筹,由北京化工大学谭天伟院士团队负责筹建运营。创新中心规划布局生物发酵中试、生物反应中试、生物分离及转化中试、分析测试平台四个支撑平台;建设生物制造产品创新中心、生物制造原料开发中心以及生物催化剂设计中心三个分中心。成果孵化空间规划建设生物实验、测试平台及办公空间等标准化生物制造产业空间,用于承载合成生物创新企业入驻。
北京市合成生物制造技术创新中心(筹)相关负责人、北京化工大学高新院副院长王斌表示,生物制造处于产业变革前夕,合成生物已成为驱动产业创新、升级的重要抓手,创新中心通过链接高校资源、科研机构和企业,满足社会及产业所需,希望通过推动合成生物产业发展,帮助更多产业降低原料成本、终端产品价格,使高端产品更加亲民化。
王斌介绍,创新中心围绕生物制造产业链、创新链、价值链开展全流程技术攻关,实现更多“从0到1到10”的突破,弥补产业链短板,释放生物制造潜力,为引领生物制造产业创新发展筑牢基础支撑。
北京市合成生物产业的顶层设计也逐渐完善。2024年9月,北京市科学技术委员会、中关村科技园区管理委员会会同北京市发展改革委、北京市经济信息化局联合印发实施《北京市加快合成生物制造产业创新发展行动计划(2024-2026年)》(简称“行动计划”)。
行动计划提出,到2026年,北京合成生物制造的创新资源集聚力、产业创新策源力、示范应用引领力、区域辐射带动力将全面提升,北京创新策源、津冀承接支撑、辐射带动全国的发展格局基本形成。
届时,北京市将在重点应用领域落地一批创新产品,新增3家合成生物制造上市企业,引育5-10家具有国内外影响力的领军企业,培育百家以上优秀初创硬科技企业,初步形成1-2个百亿级产业集聚区。
据了解,目前,北京市已集聚80余家合成生物制造领域创新企业,部分化工、食品、医药等领域的在京重点央国企也在积极布局新赛道,创新成果加速涌现。
其中,齐禾生科改造的高油酸大豆,油酸含量从20%提高到80%。微构工场首次实现嗜盐菌工程改造,大幅减少了其他细胞工厂所需要的发酵成本,实现聚羟基脂肪酸酯(PHA)产业化。衍微科技基于自主知识产权的红球菌底盘菌技术,多种原料的生物合成表达量达到全球领先。首钢朗泽利用工业尾气为原料生产微生物蛋白,2023年产量达到乙醇9万吨、蛋白1万吨。
新京报贝壳财经记者 丁爽
编辑 王进雨
校对 陈荻雁