上海超级工厂极致的效率一直被视为是业界标杆。作为中国首个外商独资整车制造项目,也是特斯拉首个在美国之外的超级工厂,长期以来一直坚持助力对区域及城市发展,积极为“中国智造”走出海外作出贡献。2023年,特斯拉上海超级工厂全年交付量达到94.7万辆,同比增长33%,占特斯拉全球交付量的一半以上。
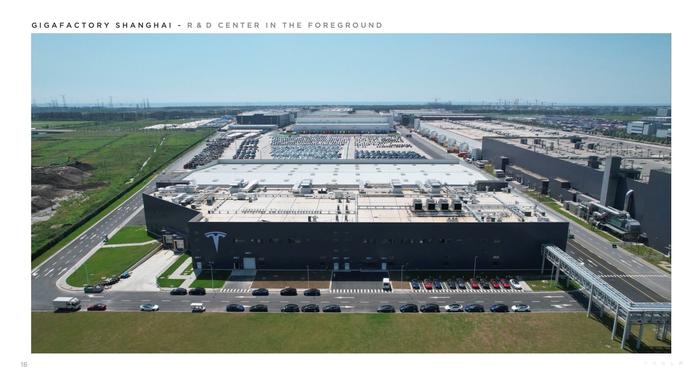
4年来,包括特斯拉上海超级工厂在内,临港的新能源汽车年产值已突破2300亿元。 在特斯拉的拉动下,临港新片区已经构建起涵盖汽车芯片、自动驾驶系统、汽车内饰、车身、新材料、精密加工等新能源车全生态领域的“安全、自主、可控”的产业生态,成为首个千亿级产业。预计到2025年,新片区智能新能源车产业规模将突破3000亿元,成为具有全球影响力的智能新能源车产业集聚地。
特斯拉上海超级工厂在极短的时间里实现了零部件本土化率达到95%以上,带动超过400家本土供应商,并帮助超过60家中国供应商成功进入特斯拉全球供应商体系,对我国新能源汽车产业链完善、技术提升、规模扩大、成本降低发挥了积极的带动作用。
上海超级工厂也已经成为特斯拉全球产能最大的电动车生产基地之一,并成为特斯拉重要的出口中心,数据显示,中国每出口两辆电动车,就有一辆来自特斯拉上海超级工厂。 依托着中国完善的供应链体系和一流的“中国智造”能力,生产出全球领先的高品质智能电动车Model 3及Model Y,销往欧洲、亚太多个国家和地区,受到海外车主的热烈欢迎和广泛赞誉。
30多秒就有1辆车下线
作为特斯拉全球重要出口中心的上海超级工厂,也是特斯拉首个在美国以外的工厂,对特斯拉深耕中国和全球市场有着极为重要的战略意义。特斯拉2023年年产能已提升95万辆/年以上。目前,上海超级工厂已实现零部件本土化率超95%,部分车间自动化率已达到95%,30多秒就能下线一台车。生产制造是特斯拉难以被复制的核心竞争力。
上海超级工厂在建设之初就进行了长远科学的规划和设计。上海超级工厂采用直线型设计,大幅减少了上下、转弯次数,并取消缓冲区冗余设计,制造效率大幅提升。车间内双层厂房设计,极大程度地提高了空间使用效率;几个生产制造环节被整合在一起,平面面积和立体空间均可以得到高效利用。另一方面,自动化产线让特斯拉生产效率极大提升,以往数千人才能完成的传统生产线工作效率,如今特斯拉只需要几十人即可完成。 比如,在特斯拉焊装车间,自动化率已经接近100%。

特斯拉上海超级工厂应用的6000吨级压铸机,在焊接流程中大大简化了Model Y车型后底板的连接工艺,使车身焊点和涂胶量都大幅降低,将原本需要70多个零件焊接件组成的后底板一次压铸成型。 制造时间由传统工艺的1-2小时缩减至3-5分钟,大幅减少了生产线和基础设施的需求,简化了生产流程,缩短了生产时间。生产效率得到大幅提升。 一体化压铸工艺在特斯拉的首开先河下,引发了车身制造的技术变革,俨然已经成为车企们的发展方向。继特斯拉之后,不少企业紧跟其后,也开始跟进布局和规划应用一体化压铸技术。
特斯拉独特的Warehouse On Wheel(轮子上的仓库)物流系统,通过流动的集装箱仓库省却了几乎所有的仓储面积。特斯拉没有在车间或厂区内建设仓库,用流动仓库代替固定仓库。卡车运送载满物料的集装箱到车间,直接将集装箱卸在车间外部“凿”出的“码头”(dock)上,接着再去运送其他物料。

特斯拉先进的自动化生产线和智能化生产流程大大提高了生产效率。比如,厂区内每天都有数千辆物流车穿梭往来,而特斯拉也在通过一套非常精细的电子管理系统,来进行车辆路线的规划。
同时,特斯拉采用了垂直一体化的生产模式,自主研发和制造电池、电机、电控等核心零部件,从而实现了整车生产的自主可控。这种高度集成化的生产方式使得工厂运作更加高效,大幅缩短了生产周期。
“抽丝剥茧”的质量管理体系
2023年6月,马斯克在特斯拉上海超级工厂说,在全球范围内,上海超级工厂不仅是效率最高的工厂,也是制造品质最优的工厂。
整个质量管控由3大基本面共同支撑:数字化、智能化的生产制造控制系统、细致又严苛的质量检测环节、 Audit评审环节。
数字化、智能化的生产制造控制系统可以实现数据采集和精确追溯等功能;同时,通过多种检测检具与自主开发的测量数据分析系统相结合,在生产制造过程中进行标准化控制,确保各项质量符合标准且可追溯;Audit评审这一人工检验方式则以用户角度出发,对已确认合格的整车进行随机抽样质量评价,确保每台车都达到质量要求。
当车辆下线后,则由售后质量管理开始“接管”。从车辆下线出厂开始,从物流运输环节、交车前检查环节、交付后客户使用环节,全面呵护车辆的质量表现和客户的用车感受,快速响应市场抱怨,高效解决客户需求。
正是这“抽丝剥茧”的质量管理体系,实现了全过程质量数字化监控、智能化分析和预防工作,真正让消费者用的放心。
废弃物93%可回收,100%无害化处理
2022年年底,上海市经济信息化委员会和上海市发展改革委员会联合组织开展绿色制造示范名单评审工作,从基础设施、管理体系、能源资源投入情况、环保节能措施、产品情况以及环境排放情况等多个维度,评选确定《上海市2022年度绿色制造示范名单》。其中,特斯拉上海超级工厂荣获“上海市2022年度五星级绿色工厂”称号。
特斯拉上海超级工厂在建厂之初就贯彻可持续设计理念,通过合理规划制造布局和生产线,缩短制造过程中的物流周转路径、优化场地使用率,从而降低物流过程中产生的碳排放,在追求高效的同时坚持节能减排,旨在成为“绿色工厂”的典范,并把环保贯彻到每一个生产流程之中。
上海超级工厂2022 年产生的所有废弃物中,93%可回收。同时,2022年,上海超级工厂工业固体废物资源再利用率达93%以上,实现100%无害化处理。同时,92% 电池原材料金属可实现再利用,纸张、塑料和金属等日常废弃物回收率高达 96%。工厂也在努力减少固体废弃物的产生,通过零部件循环包装的使用,每年减少废弃物4.5万吨以上。
工厂也从源头减少废水的产生和排放。空压站、冷冻机组、焊接机器人等冷却过程,均采用循环冷却水,工业用水循环利用率高达98%,每年可实现回收中水超过40万吨。排放废水中绝不含有一类重金属,避免重金属环境污染。
上海超级工厂也通过持续精进绿色工艺,减少废气排放。从选材阶段开始就严格贯彻环保理念。以涂装车间为例,该车间全部采用低 VOCs(挥发性有机物)涂料产品,采用“两涂一烘,免中涂”工艺,除清漆外均采用水性涂料,进一步降低废气产生。涂装车间烘干废气均采用 RTO(Regenerative Thermal Oxidize,蓄热式焚烧)处理工艺,将高污染废气转化为低污染物质,处理效率高达97%。工厂内燃烧器均采用低氮燃烧技术,有效降低氮氧化物的排放。
“4小时供应链”体系横跨江浙沪
特斯拉上海超级工厂零部件本地化率、供应链本土化率均超过95%,仅签约的本土一级供应商就有约360家,特斯拉把其中约60家企业带到了国际市场,它们也获得了其他国际汽车厂商的认可。特斯拉“4小时供应链”体系横跨江浙沪三地,从临港新片区向外辐射至苏州、宁波、南通等长三角地区,涵盖电池、汽车芯片、自动辅助驾驶系统、汽车内饰、精密加工等新能源车零部件的全生态链,实现产业生态的“安全、自主、可控”。
上海超级工厂带来的“集群效应”进一步拉动临港及上海的相关产业发展。2021年5月,18个智能新能源电动车产业项目集中签约落地临港,总投资超过160亿元;同年,智能新能源车产业发展成为该片区的千亿级产业集群。2023年,临港新增签约特斯拉储能项目、长电芯片封测项目等重大前沿产业项目86个,总投资达885亿元。临港新片区管委会提供的数据显示,4年来,包括特斯拉上海超级工厂在内,临港的新能源车年产值已突破2300亿元。
创新人才培养机制
在本土化战略下,特斯拉不断输送新能源汽车人才,为中国智能汽车正向研发体系贡献力量。目前,特斯拉上海工厂人员规模已超过2万人,其中中国员工占比99.9%以上。
特斯拉已将人才布局提升到企业战略的高度,正在持续培养从一线操作人员到高端技术人才、新能源行业管理人才的全产业链人才储备。
特斯拉创新人才培养机制,积极参与国家产教融合试点项目,通过校企联合培养、新型学徒项目等方式多渠道培养高水平技能人才,促进教育链、人才链与产业链、创新链的全方位融合。截至2022年底,特斯拉在中国已累计组建 20 个校企合作班,定向培养 670 名学员;新型学徒项目参与学员超过 900名,近150人通过成人高考考入合作院校成人本科,完成学业并表现优秀的,将享受特斯拉专门的奖学金。
无论是合作伙伴、还是行业人才,集聚在特斯拉周围的这群志同道合的“伙伴们”,持续精进生产能力、不断研发前瞻技术,推动电动车行业焕发十足活力。特斯拉正在用实际行动助力中国智造和人才培养。